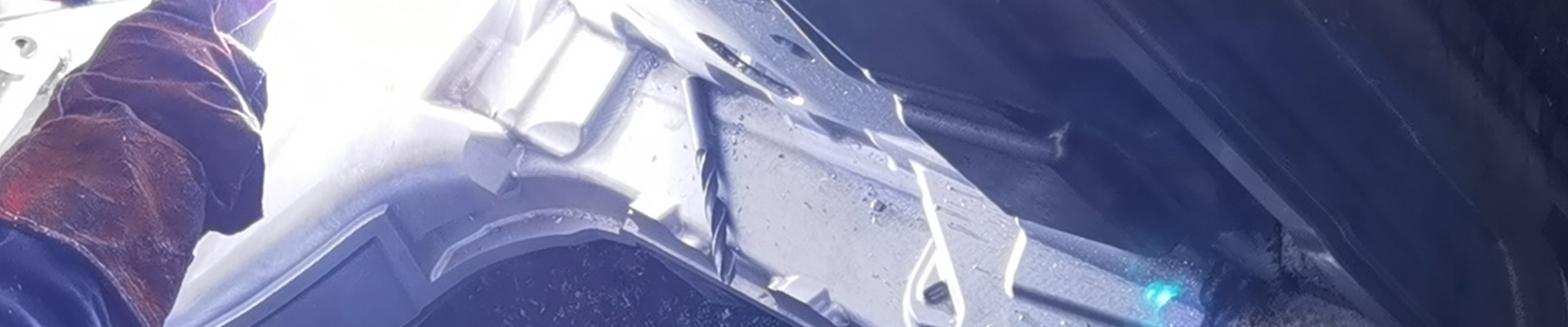
- Bolg -
19
2025
-
03
Sustainable Practices in CNC Casting Drive Industry-Wide Shift Toward Eco-Conscious Manufacturing
Author:
A quiet revolution is transforming CNC casting facilities worldwide as environmental imperatives reshape traditional production methodologies. Groundbreaking research reveals that optimized CNC strategies can reduce energy consumption in post-casting operations by 53% while maintaining stringent quality standards.


WE LOOK FORWARD TO SERVING YOU!
Taizhou Jingzhen Mould Technology Co., LTD.
Add:Unit 2, Building 25, Zhichuang Zhizhuan Park, Chengdong Industrial Park, Xiangshan County, Ningbo City, Zhejiang Province,China
Tel:+86-574-65762018
TEL: E-mail:
+86-137 7703 2220 (Zhang Meize) zmz@jinzeen.net
Wechat /Whatsapp is the same as the mobile phone number
+86-135 8680 0098 (Zhao Xia) zx@jinzeen.net
Wechat is the same as the mobile phone number
+86-159 5743 0850 (Ye Weizong) ywz@jinzeen.net
Wechat is the same as the mobile phone number
+86-158 6758 3965 (Zhou Jie) zj@jinzeen.net
Wechat is the same as the mobile phone number
+86-139 6836 6133 (Wang Chunying) wcy@jinzeen.net
Wechat is the same as the mobile phone number
+86-158 5810 0559 (Li shihui) summer@jinzeen.net
Wechat /Whatsapp is the same as the mobile phone number
+86-198 1689 5393 (Han Ying) sales@jinzeen.net
Wechat /Whatsapp is the same as the mobile phone number
Copyright © 2025 Taizhou Jingzhen Mould Technology Co., LTD. Powered by www.300.cn Seo Business license