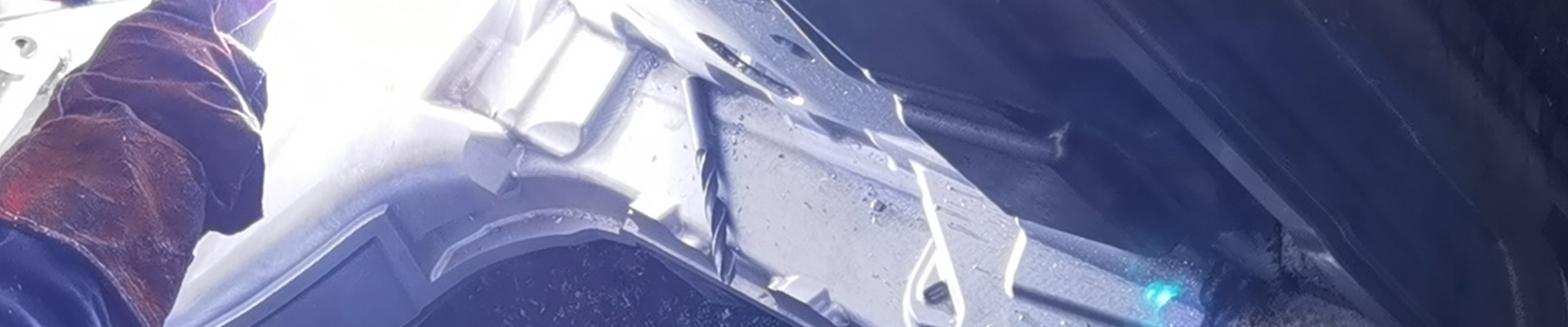
- Bolg -
19
2025
-
03
Rising Demand for Complex Cast Parts Spurs Innovations in CNC Casting Automation and Scalability
Author:
Explosive growth in sectors requiring geometrically intricate metal components is propelling unprecedented advancements in CNC casting automation.


Previous page
WE LOOK FORWARD TO SERVING YOU!
Taizhou Jingzhen Mould Technology Co., LTD.
Add:Unit 2, Building 25, Zhichuang Zhizhuan Park, Chengdong Industrial Park, Xiangshan County, Ningbo City, Zhejiang Province,China
Tel:+86-574-65762018
TEL: E-mail:
+86-137 7703 2220 (Zhang Meize) zmz@jinzeen.net
Wechat /Whatsapp is the same as the mobile phone number
+86-135 8680 0098 (Zhao Xia) zx@jinzeen.net
Wechat is the same as the mobile phone number
+86-159 5743 0850 (Ye Weizong) ywz@jinzeen.net
Wechat is the same as the mobile phone number
+86-158 6758 3965 (Zhou Jie) zj@jinzeen.net
Wechat is the same as the mobile phone number
+86-139 6836 6133 (Wang Chunying) wcy@jinzeen.net
Wechat is the same as the mobile phone number
+86-158 5810 0559 (Li shihui) summer@jinzeen.net
Wechat /Whatsapp is the same as the mobile phone number
+86-198 1689 5393 (Han Ying) sales@jinzeen.net
Wechat /Whatsapp is the same as the mobile phone number
Copyright © 2025 Taizhou Jingzhen Mould Technology Co., LTD. Powered by www.300.cn Seo Business license